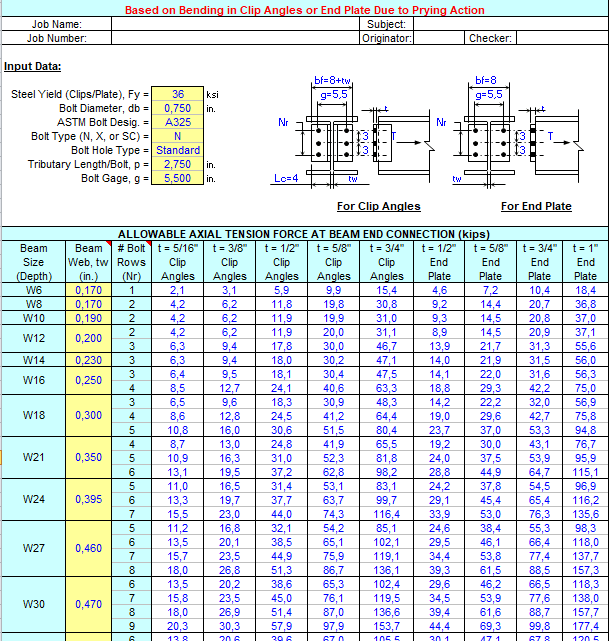
Prying Action Analysis Excel Sheet
8 May 2025 Off By The Engineering CommunityTable of Contents
Prying Action Analysis Excel Sheet
In structural engineering and construction, prying is a critical phenomenon that can compromise the performance of bolted connections and reduce the safety of steel structures. Prying action often goes unnoticed in design but can lead to severe failures under certain loading conditions. Understanding prying forces, how they develop, and how to prevent them is essential for civil engineers, contractors, and architects alike.
What Is Prying Action?
Prying action refers to an additional tensile force that develops in bolted connections when a load causes the connected plate to deform and lever against the bolt, increasing the effective tension in the bolt. This often happens when:
-
A plate or bracket is thin and flexible
-
The load is applied at a distance from the bolt (eccentric loading)
-
The joint design does not adequately resist local bending
Think of it like a crowbar effect—where a small force at one end can generate a large force at the fulcrum. In construction, this means bolts may carry more force than initially intended, leading to bolt failure or joint separation.
Common Examples of Prying in Construction
-
Steel beam-to-column connections using end plates
-
Bracket-mounted supports for piping or cable trays
-
Flange joints where bolt and plate flexibility causes lever action
-
Tension-loaded cleat connections in trusses or lattice structures
In all these cases, inadequate stiffness of the plate or connection can lead to excessive deformation and trigger prying forces.
Effects of Prying Action
Ignoring prying forces in design can result in:
-
Overstressed bolts and premature bolt failure
-
Excessive joint deformation
-
Reduced connection stiffness and load capacity
-
Catastrophic structural failure in worst-case scenarios
Prying can be particularly dangerous in seismic zones, where connections are subject to dynamic loading.
How to Prevent Prying in Construction
Preventing prying action requires thoughtful design and detailing. Here are the top methods used by engineers:
1. Use Thicker Plates or Stiffeners
Increasing plate thickness or adding stiffeners reduces flexibility, thereby minimizing deformation and prying.
2. Reposition Bolt Holes
Placing bolt holes closer to the load application point (reducing the lever arm) decreases the chance of prying.
3. Preload Bolts Properly
Preloaded bolts (tensioned during installation) can help resist prying forces more effectively than non-preloaded bolts.
4. Consider Prying in Design Calculations
Codes like AISC, Eurocode, and BS 5950 provide guidelines for including prying action in bolt tension calculations.
5. Use Finite Element Analysis (FEA)
For critical joints, engineers may use FEA software to simulate prying behavior under various loads and geometries.
Relevant Standards & Codes
Engineers should consult the following standards for detailed guidance on prying forces in structural connections:
-
AISC 360 – Specification for Structural Steel Buildings
-
Eurocode 3 (EN 1993-1-8) – Design of Joints in Steel Structures
-
BS 5950 – Structural Use of Steelwork in Building
Conclusion: Don’t Underestimate Prying
Prying action in construction may seem like a minor issue, but it has major implications for safety and performance. By understanding the mechanics of prying and designing connections that resist it, engineers can ensure robust and reliable structures. Whether you’re working on commercial buildings, industrial facilities, or bridges, factoring in prying action is a best practice you can’t afford to skip.
More from my site
ASCE 7-10 Load Combinations Spreadsheet
Design Of Circular Water Tank Spreadsheet
Design Of Expansion Joint For PSC Continuous Type Superstructure Spreadsheet
Design Of Isolated Footing Under Vertical Load According to ACI 318-02 Spreadsheet
Gravity Wood Beam Design Spreadsheet
Seismic Design For Ordinary Concentrically Braces Frames Spreadsheet